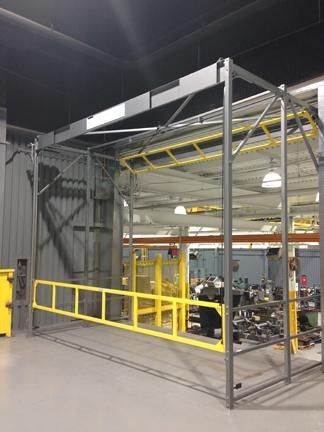
COVID-19 Medical Test Kit Equipment Manufacturer Gets Fall Protection for Priority Production
As the race to obtain more widespread testing capability for the COVID-19 virus began, a medical testing equipment manufacturer needed to increase production of its test kit supplies. The manufacturer was working with a local material handling equipment distributor to ensure it could safely and quickly ramp up production at its facility.
At the manufacturing facility, two new elevated pallet drop areas were created to handle the increase in new materials. Because the application required employees to pick the material from the pallets in the elevated drop areas close to the ledge, fall protection systems were needed to keep those employees safe.
The material handling distributor reached out to Mezzanine Safeti-Gates to discuss the high-priority project. Because of the time-sensitivity, it was imperative to find a solution that could be installed quickly. After discussing the application and area, it was discovered that the two pallet drop areas would feature pallet loads that were both extra wide and extra tall. The Roly pallet drop safety gate model was the design that would be best suited for the project because it can be easily customized for different heights and widths. Because the models would require customization, it ruled out the models available in stock, so we immediately worked to fabricate the safety gates and expedite them through the process.
The Roly is a dual-gate safety system that is configured so when the ledge gate is closed, the opposite gate is open and the material can be safely picked from the pallet drop area as the ledge gate provides a controlled access area that ensures fall protection. When the ledge gate is raised, the opposite gate closes, creating a barrier around the pallet drop area while it is being loaded and preventing workers from an exposed ledge.
To meet the manufacturer’s sanitation requirements, Mezzanine Safeti-Gates suggested the Roly safety gates be power operated so that they could be opened and closed via remote controls, which would limit the number of times the safety gate would need to be touched by employees.
While the custom safety gates were being manufactured, the material handling distributor scheduled installation of the gates in the manufacturing facility for three weeks later. Upon the arrival, the safety gates were quickly and easily installed by the distributor’s team to keep the workers at the new pallet drop areas safe from falls from upper levels. This allowed the facility to increase operations and function at maximum capacity while providing a safe environment for its employees.