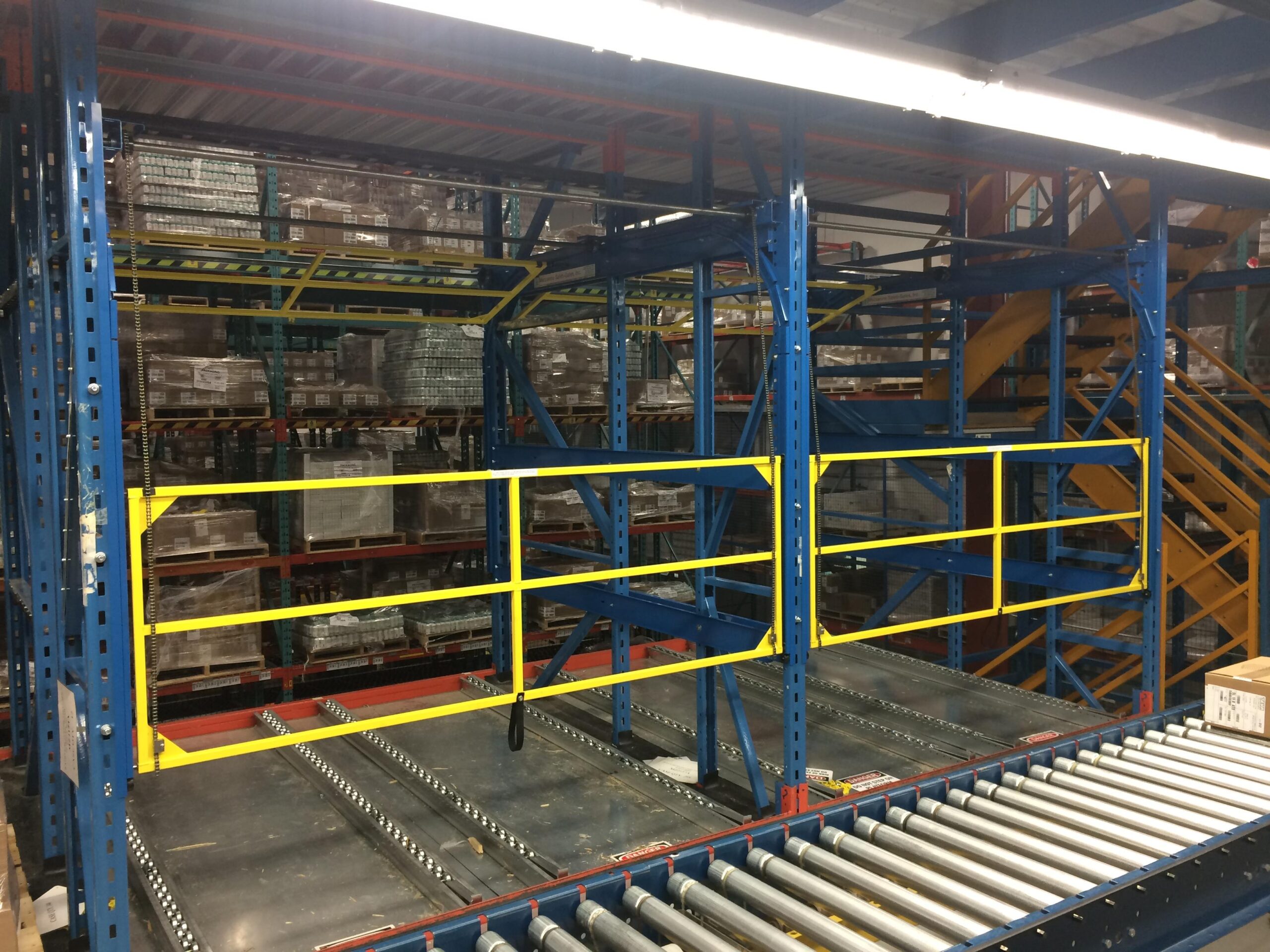
Pallet Flow Lane Safety: Good vs Best
Pallet flow lanes can greatly help the efficiency of a distribution center but they can be a nightmare for safety managers as the proper method for securing these areas can be confusing.
Pallet flow operations often look like this: the facility features a multi-level rack supported pick module where multiple deep pallets are pushed into the system. Flow rails are installed between the beams often at an angle to allow the pallets to flow into the system as they are loaded. There are typically one or two lanes in a bay, sometimes with an aisle between the lanes in a cluster picking application. Typically the picker on the platform will pick from the first pallet position or enter the lanes to pick from various pallets, putting the items on a takeaway conveyor to be packaged and shipped to individual locations.
For productivity, this is a great way to load many pallets into a system and for the pallets to be picked in a first loaded, first picked sequence, but it’s not necessarily good for safety.
No matter how the pallet flow lanes are configured, when they are in a multiple-level system there will always be a ledge that needs to be secured. Sometimes two ledges create fall hazards: the one at the end of the lane where the operator picks, and the one at the beginning of the lane where the lift truck loads. For this reason, the lanes are often decked over, which accomplishes two things. Decking fills in the ledge at the picking position and leaves only one ledge where the lift truck loads, and also prevents loose items like boxes or pieces of the pallet, from falling to the levels below where they could injure someone.
Decking is good, however, decking also creates safety concerns. With decking there is an egress into the lane. In cluster-picking applications, this egress is warranted so the pickers can pick from several pallets, but most times the operation doesn’t ask for employees to enter the lanes. In reality, the decking allows egress into the lane so now the edge of the lane must be guarded.
Safety managers know that they need to provide fall protection for employees picking within the module, and OSHA and ANSI require protection for employees working at any elevation of over four feet.
So now that you’ve decked over the flow lane and created one ledge that needs to be secured, the question is how do you secure this ledge? There are two ways the ledges of pallet flow lanes can be secured. We’ll call them “good” and “best.”
“Good” solutions are self-closing swing gates designed specifically for pallet flow lanes that the lift truck pushes open, and once the pallet flows into the lane, the gate automatically closes. The gates should be designed to accommodate the pushing of the lift truck and load, and consist of a solid panel to create a smooth transition for the pallet flowing onto the lanes. The swing gates should include tension adjustable hinges so the speed of the closing gate can correspond with the weight of the pallet loads, as well as rugged stops so the gates do not swing outward.
The two main injuries we hear about in pallet flow applications are people falling from the upper levels and pallet loads being pushed into the legs of employees when they are working in the lane. If designed correctly, this type of gate can create a safe environment – at times. When the lane is empty this type of gate will be closed, but when the lane is full the last pallet loaded will hold the gate open, creating an unsafe area. A pallet is not an acceptable fall protection barrier and it doesn’t protect employees from being inside the lane when pallets are being loaded.
The self-closing gate is an improvement over having no barrier, and while it will be in place to help prevent some fall related injuries, there also will be times when it impedes safety, which is why it is a good solution but not the best solution.
‘The “best” solution is to install a dual-gate safety system that maintains a safe environment for pickers at all times. This design uses a gate at the ledge and a second gate at the end of the lane where the picker is standing. The gates are interconnected and counterbalanced so when one gate is open, the opposite gate is closed. Operationally, the ledge is open when the lift truck loads load pallets into the lanes, which means the rear-side gate is closed, preventing employees from accessing the lane and keeping them a safe distance from the ledge. Pickers then can manually raise the rear gate, which closes the ledge gate, securing the ledge while they pick from the pallets, as well as preventing the lift truck from loading more pallets while they are in that area.
This type of dual-gate system can also be designed extra wide and extra deep to accommodate the design of the pallet flow system, and is available in a rack-supported design to attach to the existing pallet rack to maximize space in the bay and for a rugged connection that doesn’t need to get lagged down into the decking. Dual-gate systems are available for both the inbound and outbound lanes and will maintain a safe environment at all times, ensuring there is a barrier that is always in place and keeping the employees out of the lane when the lane is loaded. These safety systems meet updated OSHA codes and ANSI standards as well.
If you have questions about securing your pallet flow lanes, we’re happy to help.